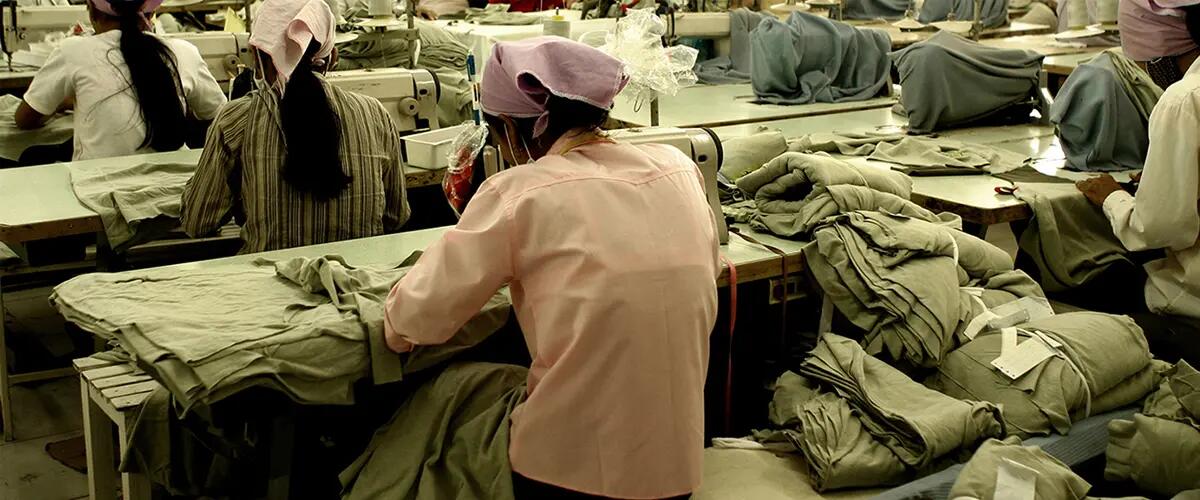
Poor labor conditions in a supply chain have the potential to create operational risks.
Labor remains a wrinkle in fashion industry's supply chain
This article originally appeared in Outsource Magazine. It was written by Katy E. Wilson, who completed Rutgers Business School's Master of Supply Chain Management program last year, and Maung K. Min, an instructor in the Supply Chain Management Department at Rutgers Business School.
In 2015, the Joint Economic Committee of the United States Congress reported that the fashion industry globally is valued at $1.2 trillion. Of that $1.2 trillion, more than $250 billion is spent annually in the United States alone and this number continues to grow. Current reports show that the retail value of the apparel and shoe industry in the U.S. was valued at almost $360 billion (and counting) in 2015.
Labor issues are material to the fashion industry because "roughly 99 percent of apparel and footwear sold in the U.S. is manufactured outside the country, typically by independent suppliers." This is attributed to the fact that apparel companies enter into contracts with manufacturers which have the lowest manufacturing costs – significantly lower than the United States. In Bangladesh, workers are paid an estimated 24-cents per hour, compared with China’s $1.26 minimum wage. Labor practices, from a supply chain perspective, become especially critical for this industry due to prevalence of "sweat shops" in these manufacturing operations. Sweat shops have been described as the following: "any factory which may have unreasonably authoritative overseers, dangerous and unhealthy (both physically and psychologically) working conditions, and enforces long hours with low pay."
Over the years there have been a lot of bad press and articles written about many apparel companies in regard to their labor practices overseas – "many Americans are unaware that their appetite for consumerism fuels a deeply controversial industry, and just as foreign-manufactured goods are often more than meets the eye, the sweatshop debate is highly intricate." Poor labor conditions within the supply chain have the potential to create operational risks in terms of the loss of capital as well as potentially cause disruptions in production due to safety incidents or worker strikes. From a public relations perspective, this can also cause damage to brand reputation as well as value. Looking at it from a government view, it can cause local governments to impose stricter regulations which will in turn increase costs of production.
All of the media attention focused around labor practices of fashion/apparel companies has caused companies to focus on this particular aspect of their supply chain as part of their corporate social responsibility in order to outline their goals on how to improve labor practices and how they plan to achieve those goals.
From a business case perspective, there is clear evidence which suggests how powerful a company’s labor practices are and just how this can affect future business. In the SASB Consumption II Brief there are two examples of this: "…reputational impacts from labor problems in the supply chain can affect demand for products. For example, in 2011, Cornell University cut contracts with Adidas after the company failed to properly pay workers in an Indonesian factory. Additionally, in 2014, Cornell cut ties with VF Corporation for deals estimated to be worth $4 million after the company failed to address worker safety issues in Bangladesh.”
Another impact is labor unrest which may lead to strikes. "Nike experienced such stoppages in 2013 and faced weeks of supply disruptions and added costs due to worker strikes over low wages in Vietnam and Cambodia." This clearly shows the financial implications companies can face when dealing with labor issues in foreign supply chains.

Nike has been one of the leaders in trying to achieve best practices within their industry which can be attributed to the criticism they faced in regard to labor practices in its supply chain in the 1990s. In the SASB Consumption II brief there are some noteworthy contributions which they have made: "In 1999, the company helped to found the Fair Labor Association, and in 2005 it became the first in the industry to publish a complete list of the factories that it contracts with. Nike currently audits and provides rankings for more than 785 contract factory locations on labor issues, including minimum age requirements, compensation practices, fire safety management, and worker hours."
Additionally, companies such as PVH and Adidas signed the Accord on Fire and Building Safety in Bangladesh. Other companies such as Wal-Mart Stores and Gap have also set out to improve working conditions in facilities in places like Bangladesh. They have achieved this by "setting up a voluntary safety standards organization known as the Alliance for Bangladesh Worker Safety. Through a $42 million fund, the organization hopes to improve factories’ access to capital for safety upgrades."
For the future of the topic of labor within the supply chain of the fashion/apparel industry, there will be a focus on the continued improvement on the issues which surround labor in manufacturing facilities overseas. There are two paths in which the continued improvement can be carried out: either by companies taking on the initiative of creating standards and organizations which promote fair labor practices in manufacturing facilities; or having regulations imposed on them by governmental agencies in host countries in which they are manufacturing goods.
We should expect to see more meaningful disclosure in companies SEC annual filings. Currently, 10 percent of the companies in the fashion/apparel industry provide no disclosure in their SEC annual filings, and 50 percent provide only boiler plate disclosures. This leaves only 40 percent which supply industry-specific information on labor conditions within their supply chains.
Over the past two decades there have been great strides and progress made in improving labor standards in manufacturing facilities overseas. This is a topic which has received a great deal of attention due to the negative press surrounding many fashion/apparel companies based here in the United States. This is also true for other industries as well such as the electronics and toy industries. Companies really need to ask themselves if making an extra 50 cents in profit on a product manufactured is worth sacrificing the health and safety of the workers who produce those products in offshore manufacturing facilities. With the push for companies to publish their corporate social responsibility goals and achievements, this allows visibility to everyone on what exactly is being done in relation to labor issues. The public does not have to wait for a scandal to break before learning what companies are doing but can educate themselves on a daily basis and determine whether or not they would like to buy a company’s products or services based on their investments in corporate social responsibility.
Photo credit: Liuser/iStock/Thinkstock
Press: For all media inquiries see our Media Kit